Total Solution for Structural Optimization
OPTISHAPE-TS
Shape Optimization
Non-Parametric Shape Optimization
OPTISHAPE-TS is the business software which contains the nonparametric shape optimization technique by "Traction method".
Nonparametric Shape Optimization proposes the most suitable shape by changing surface shape.
By Traction Method, it needs just the boundary condition.
So the user can easily use this software at various design stages like the detailed design stage, the improvement stage of existing parts, etc.
Cost Functions
- Volume
- Mass
- Moment of Inertia
- Surface Area
- Center of Gravity Position
- Maximum Thermal Stress(Mises)
- Thermal Displacements
- Temperature
- Standard Diviation of Temperature Distribution
- Heat Flux on Temperature-fixed Point
- Static Stiffness
(Compliance) - Maximum Mises stress
- Maximum principal stress
- Minimum principal stress
- Maximum principal strain
- Miminum principal strain
- Maximum principal shearing stress
- Maximum displacement
- Displacement
- Eigen Value/natural frequency
- Displacement of Vibration Mode
- Displacement Square Error of Vibration Mode
- Amplitude
(Displacement/Velocity/Acceleration) - Amplitude of Velocity in Normal Direction
- Buckling Load Factor(Eigenvalue buckling)
- Amplitude of Equivalent Alternating Stress(Fatigue)
- Non-linear Campliance
(Geometric nonlinearity)
In addition, it is equipped with many other functions.
Analysis case
Lightweighting of Aluminum Wheel
It gives the lightweighting shape as considering stress,stiffness and the production requirements.
- Object : Volume Minimization
- Constraint : Stiffness, Shape Restriction
Stress Minimization of Link Arm
It minimizes Mises Stress while fixing volume.
- Object : Mises Stress Minimization
- Constraint : Volume
Natural Frequency Maximization of Lower Arm
It gives the shape which maximizes the natural frequency of the specified vibration mode.
Therefore, it can improve the vibration characteristic.
- Object : Natural Frequency Maximization
- Constraint : Volume
Production Requirements
The various features, such as cost functions for production requirements, shape restrictions, and shape constraints, enable optimization that considers manufacturing requirements.
For example, considerations include die-drawing and thickness limitations for forging and casting processes, specifying designable areas based on interfering components, and incorporating symmetries such as planar and rotational symmetry.
This approach enables the optimization of shapes while adhering to various production constraints.
- Specifying Uniform Cross Section
- Considering Die drawing
- Maintaining Minimum thickness
- Maintaining Maximum thickness
- Specifying designable areas
- Considering interfering parts
- Ensuring uniform thickness
- Maintaining rib shape
- etc.
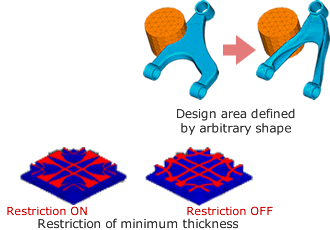